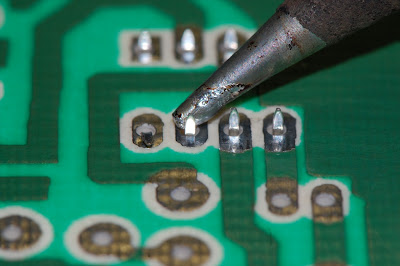
- Never touch the element or tip of the soldering iron. They are very hot (about 600°F) and will give you a nasty burn.
- Always return the soldering iron to its stand when not in use. Never put it down on your workbench, even for a moment!
- Work in a well-ventilated area. The smoke formed as you melt solder is mostly from the flux and quite irritating. Avoid breathing it by keeping your head to the side of, not above, your work.
- Wash your hands after using solder. Solder contains lead which is a poisonous metal.
- Place the soldering iron in its stand and plug in. Set the knob on the soldering iron station to a starting level of 4. The iron will take a few minutes to reach its operating temperature of about 600°F.
- Dampen the sponge in the stand. It should be damp, not dripping wet.
- Wait a few minutes for the soldering iron to warm up. You can check if it is ready by trying to melt a little solder on the tip.
- Wipe the tip of the iron on the damp sponge. This will clean the tip.
- Melt a little solder on the tip of the iron. This is called 'tinning' and it will drastically help the heat to flow from the iron's tip to the joint. If it seems to be taking a long time for a joint to heat up it is most likely because the tip is not tinned.
Inserting the component
- Bend the leads of the component to fit in the holes in the board if necessary.
- Insert the component into the board. IMPORTANT make absolute sure that the component you are placing is in the correct location and the correct orientation. Some of the components must be soldered in a certain orientation in order to function.
- If possible, bend the leads of the component outward once they are inserted into the board. This will keep the component from falling out if you turn the board upside-down.
You may wish to place many components consecutively, and then solder them all. This will save you time.
How to solder
- Hold the soldering iron on the rubber handle like a pen. NEVER touch the hot metal element or tip.
- Touch the tip of the tinned soldering iron onto the joint to be soldered. Make sure it touches both the component lead and the track. Hold the tip there for a moment.
- Feed a little solder onto the joint.
- Apply the solder to the joint, not the iron.
- Solder should flow smoothly onto the lead and track to form a volcano shape as shown in the diagram. The track and lead should literally suck up the solder.
- If the solder balls up and does not seep into the joint, allow more time for the joint to heat until you see the solder flow or seep into the joint. Do not add more solder.
- Remove the solder wire, then the iron, while keeping the joint still. Allow the joint a few seconds to cool before you move the circuit board.
- Trim any long leads sticking out the bottom of the board.
- Inspect the joint closely.
- The joint should look shiny and have a 'volcano' shape.
- If the joint has a dull texture, you will need to reheat it and feed in a little more solder. This time ensure that both the lead and track are heated fully before applying solder. Also, make sure not to move the lead while the joint is solidifying.
- If the solder looks like a blob you will need to either reheat the solder so that it may bond completely with the joint, or if there is just too much solder on the joint you may need to remove some solder using a desoldering device.
Note: With practice and an iron set at the correct temperature, you should be able to solder a joint every one to two seconds.This is how you should position the solder and the iron when making the joint:

A good Joint should look like this:

If the joint is dull or bulged, remelt the solder:


Source [Cal Poly Robotics Club]
pak klo sy mau kursus elektronik gmn?
ReplyDeletewelly